Overview
This page describes a test to determine the fuel use (MPG) penalty for adding..
- A large roof rack for mounting PV panels and other things
- A PV panel mounted directly to the roof of the van
The roof rack is a fairly large one of about the same size as some commercial and DIY roof racks used to mount arrays of PV panels, or other stuff to the roof. The PV panel is a single large 315 watt panel which is mounted in such a way as to (hopefully) reduce drag.
I am the biggest fan of solar, but it has occurred to me that the aero drag created by the solar panel mounted to the roof might outweigh the advantages and energy saving of the solar panel. This test is intended to shed some light on this.
Van Setup
Simulated Roof Rack
I had planned to just run the MPG test with my current large PV panel against the van without PV panel. But, I figured since I was going to this much effort, might as well test a larger roof rack as well. So, I made a roof rack out of scrap lumber so it could be compared to the PV panel on roof. In all cases my Maxfan was on the roof.

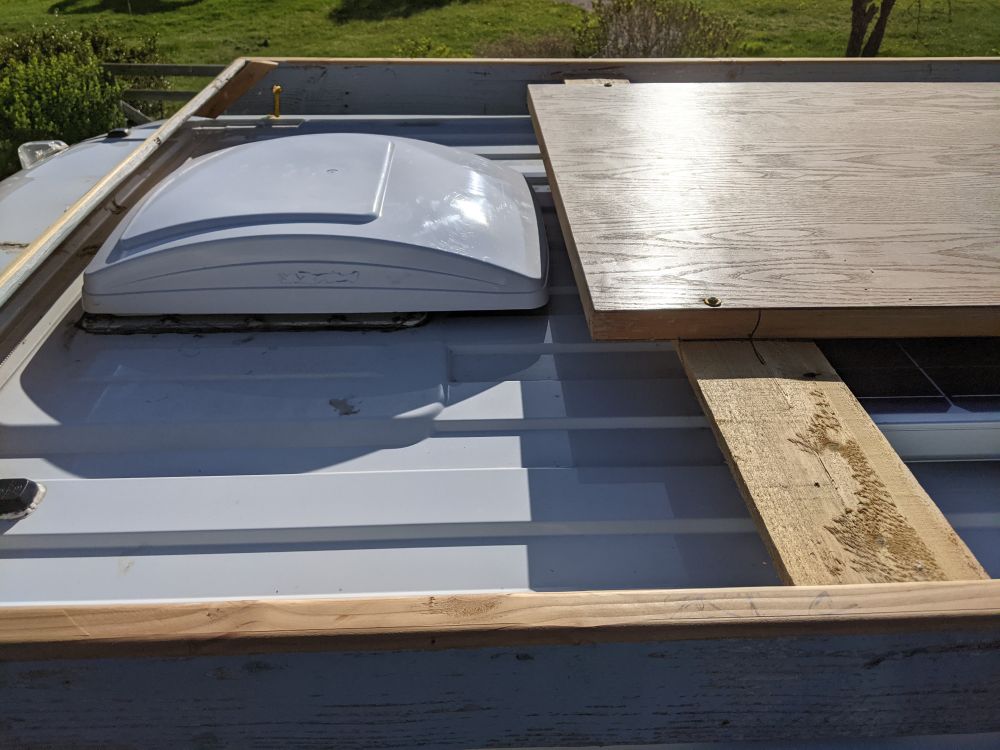
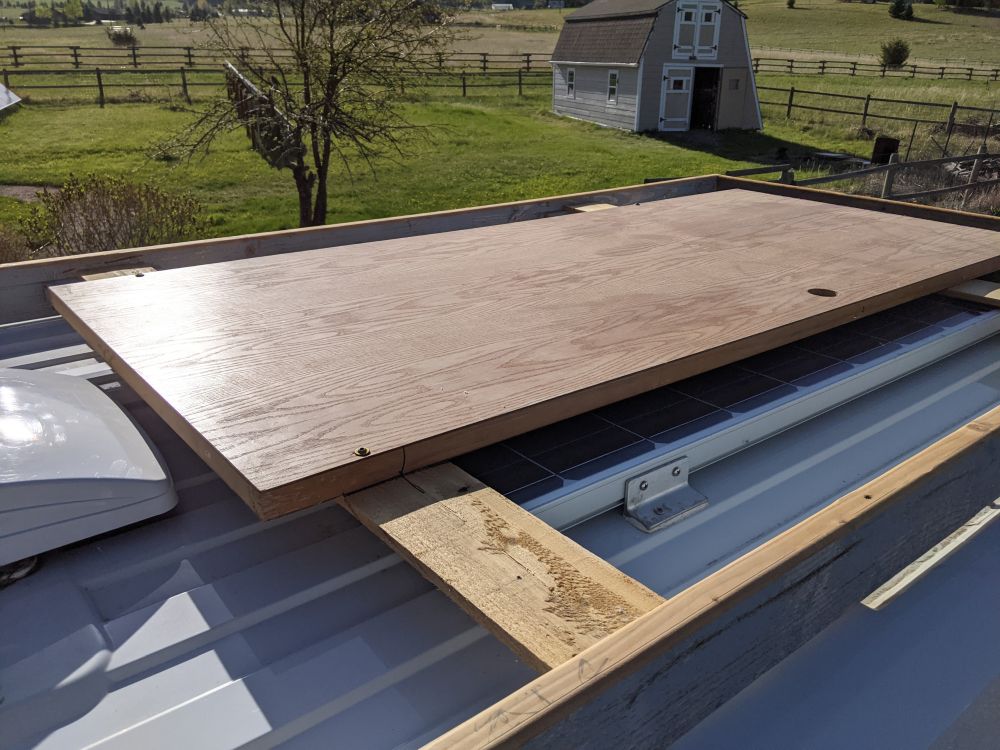
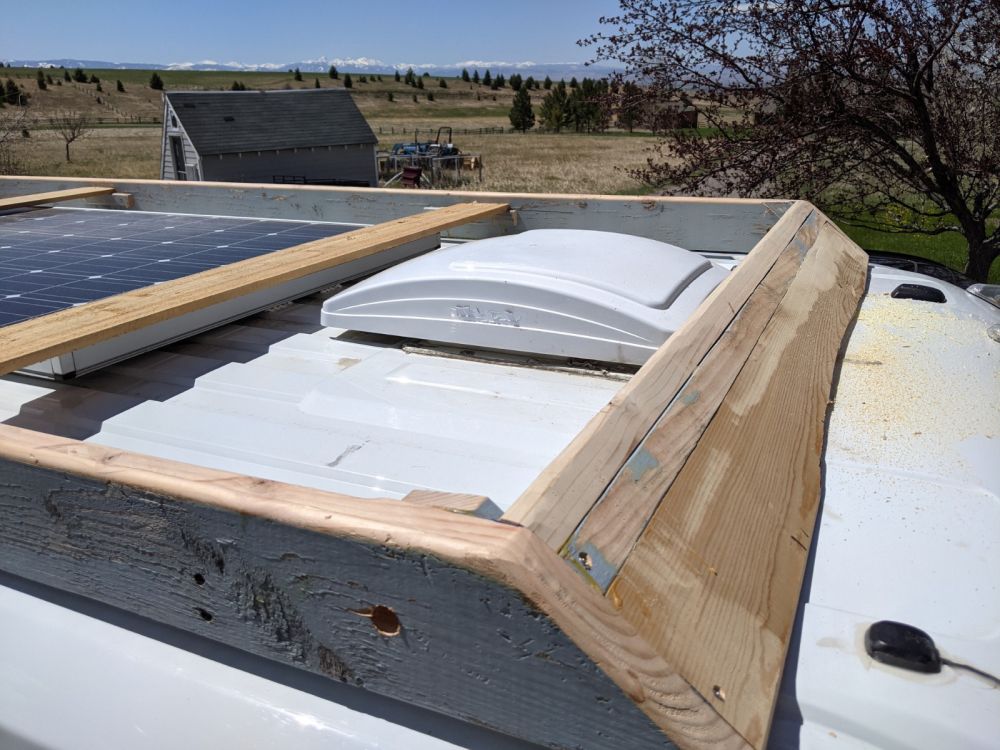
I know this looks kind of goofy, but its what I could do with scrap lumber I had in hand to simulate a roof rack. The idea is to get about the same frontal area and shape of some existing commercial racks I’ve seen. The door slab mounted on the rack simulates a PV panel that might be mounted on the rack. The rack is 4.5 inches tall by 61 inches wide by 118 inches long. Its held down to the van by ropes at each corner for easy removal with no holes.
The roof rack increases the frontal area of the van by about 4.5%, but maybe more importantly, it increases the drag coefficient of the van — both contribute to increased drag and lower MPG.
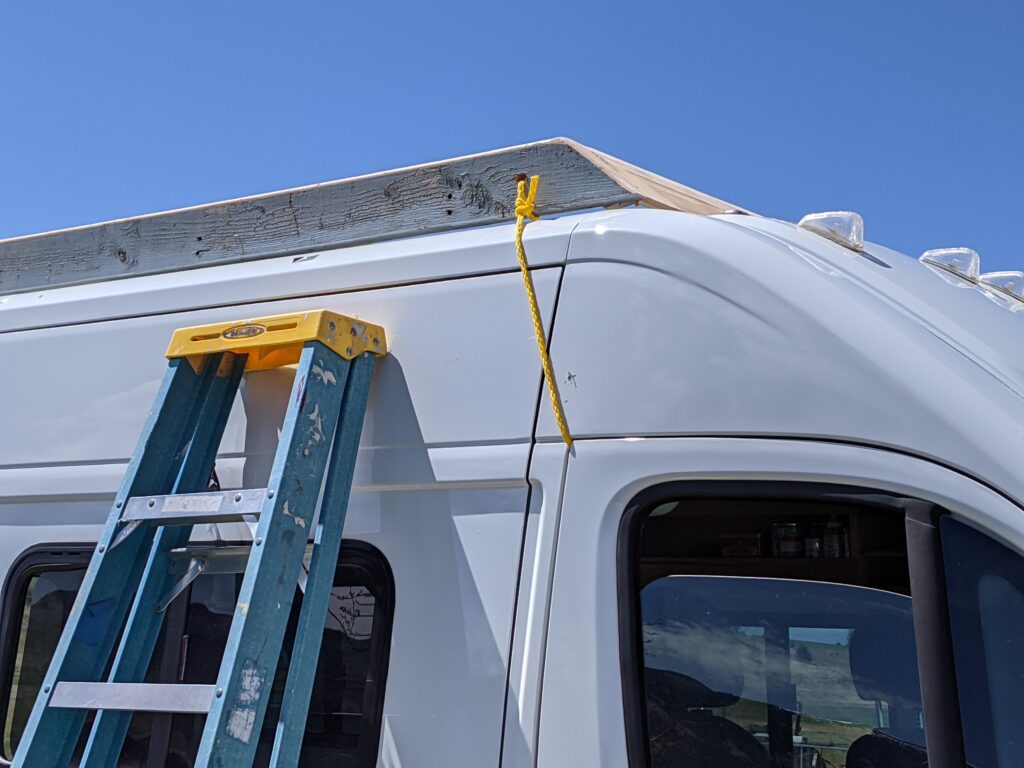
The highly sophisticated roof rack mounting method.
PV Panel
This the the large single PV panel that I’ve had mounted on my van since 2014.
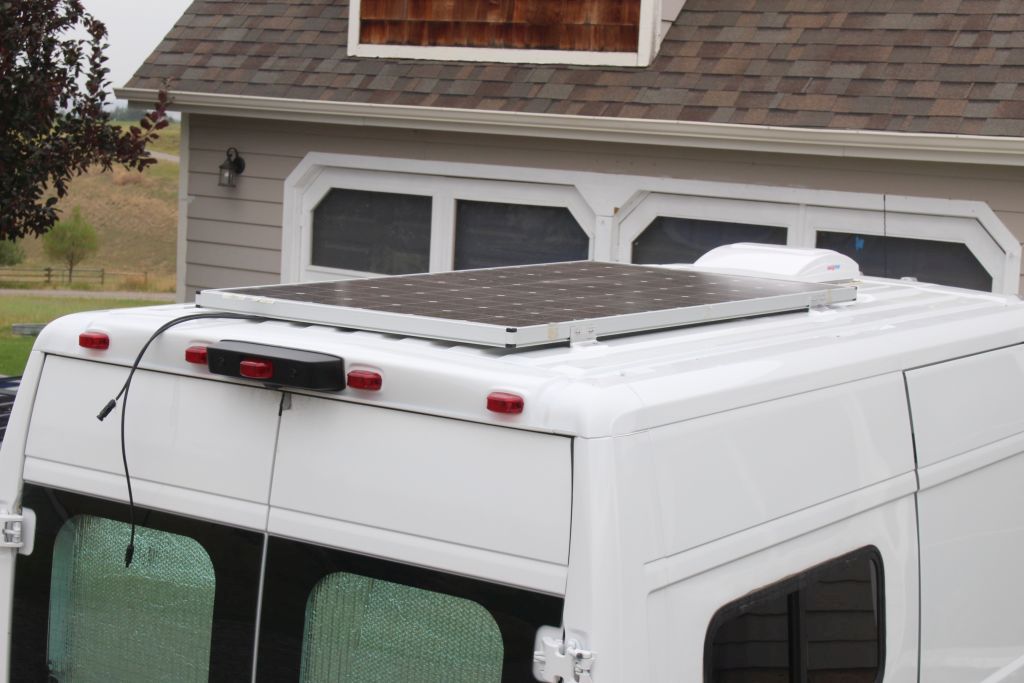
The panel is 78 inches long by 39 inches wide by 1 3/4 inches thick. I tried to mount it for low aero drag — that is, lengthwise behind the fan and nearly touching the van roof. Details here…
Bare Roof
The final configuration tested was the van with just the Maxfan installed, and the roof bare otherwise. It would have been nice to remove the Maxfan, but too much work for this time.
Test Procedure
All of the testing was done over about three hours on a low wind, sunny day.
Tires were inflated to 65 psi cold – tire pressure was up to 70 psi for actual test. The van and tires were warmed with an I90 run of 20+ miles before the start of testing. Wind speed was down around 2 mph, and since each run had an east to west followed by a west to east segment, wind effects should be minimal.
Each run consisted of a 65.2 MPH run west on I90 between two mile markers, followed by a run east between the same mile markers at the same speed. The PM Trip Computer was used to record the MPG between the mile markers. The length of the run in each direction was 12 miles. The cruise control was used during the full run.
The I90 section used had some flat areas and some modest hills. The van shifted down from 6th gear to 5th gear for short periods on a couple of the small hills. Pretty typical interstate highway driving.
A full run consisted of these steps…
- Enter I90 at interchange 288 (Manhattan, MT) going west
- “resume” cruise control at 65.2 miles per hour (or set at 65.2 if old setting was lost)
- As mile marker 288 is passed, reset Trip A computer.
- Drive with as little interference as possible to end mile marker (276) – 12 miles in all.
- Note Average MPG on Trip A while passing mile marker 276
- Exit at interchange 274 (hwy 287)
- Go across I90 and enter I90 going east
- “resume” cruise control at 65.2 miles per hour
- As mile marker 275 is passed, reset Trip A computer.
- Drive with as little interference as possible — 12 miles in all.
- Note Average MPG on Trip A at mile marker 288.
- Exit I90 at interchange 288.
Each of the three configurations were tested with two of these runs on I90 – six runs total for 144 miles total.
After the first two runs with the full roof rack, I pulled off the road at exit 288, pulled the roof rack off, and stowed it in the van. This left the van with the roof fan and my regular PV panel (39 by 78 inches). I then did two identical runs with the PV panel. I pulled off the road again and removed the PV panel, so that the only thing left on the roof was the roof fan. I then did two more identical runs in this configuration. About 3 hours total. I only had to reset the cruise control once during the whole process, and got it back to 65.2 MPH using the digital readout on my OBD app.
Since all the racks were stowed in the van, there was no change in van weight over the test except for a few pounds of gasoline used. In reality, the large roof rack would also suffer a small hit in MPG due to the weight of the rack – maybe about 0.1 MPG for a 100 lb rack.
I think this works out pretty well as a test method. Resetting the Trip Meter at the start mile marker while already having established stable cruise control speed, and then noting the Trip Average MPG while passing the end mile marker takes away the inconsistencies that would come from including the the less consistent acceleration and deceleration at the start and end of each run. On the previous MPG test for the vortex generators, I also did very careful gas fillups after each two runs as a check on the trip computer, but the two agreed well, so I did not do the fillups this time.
Of course the trip computer on most ProMasters tends to be a bit optimistic, but this does not matter when we are only comparing runs with and without the racks. In the past, when I’ve tested my trip computer, it has been about 0.5 MPG optimistic.
Results
The average MPG with full roof rack was18.75 MPG
The average MPG with PV panel was 21.1 MPG
The average MPG with no paels was 21.2 MPG
So, the full roof rack was 2.5 MPG worse than the roof with only the Maxfan on it.
Over a 200,000 mile van life, this is 1233 gallons extra gas, or at $3 per gallon $3700 in gas, and 12 tons more of CO2 emissions.
About a 12% decrease of MPG compared to the roof with only the Maxfan on it.
The PV panel was 0.1 MPG worse than the roof with only the fan on it.
Over 200,000 mile van life, this is 45 gallons extra gas, or at $3 per gallon $135 in gas, and about half a ton more of CO2 emissions.
The drag penalty for the PV panel over the roof with just the fan seems small to me. I guess its possible that mounting it low to the roof, far back on the roof, with long axis parallel to the van, and in the drag shadow of the fan all worked splendidly and the drag increment is really only 0.1 MPG. Or, maybe the random variations from run to run added up to favor the PV panel. Or, maybe some of each?
It would have been nice to test the bare roof with no fan — maybe some day 🙂
These are the run by run MPG numbers…
Roof Rack 1 | Roof Rack 2 | PV 1 | PV 2 | Bare 1 | Bare 2 | |
West run | 18.3 | 19.7 | 22.6 | 21.9 | 23.4 | 21.8 |
East Run | 18.5 | 18.5 | 19.6 | 20.2 | 19.4 | 20.1 |
I could not find a lot out there on the internet about previous drag tests of roof racks — if you know of any material, please let me know.
This paper: Impact of vehicle add-ons on energy consumption and greenhouse gas emissions Harun Chowdhury*, Firoz Alam, Iftekhar Khan, Victor Djamovski, Simon Watkins
Shows wind tunnel results for various roof mounted stuff, including roof racks. It shows a 20% increase in vehicle drag for one roof rack configuration — substantially more than our test.
Another interesting roof rack post from the EcoModder site with some testing…
Another consideration is the effect of speed. These tests were done at 65.2 MPH. If you speed up to 80 MPH, the drag force goes up by the square of velocity, so it would be up by a factor of (80/65.2)^2 = 1.5. If you assume that at 65 MPH, the aero drag makes up 70% of the total resistance (tire rolling resistance being most of the rest), then you would expect total resistance on speeding up to 80 MPH to go up by a factor of 1.35 and the MPG to go down by the same factor – maybe 14 MPG. On the other hand, if you slow down, MPG improves just as rapidly.
Thoughts on Roof Rack Drag
It seems that just from this little test you could conclude that …
- Roof racks can have a significant impact on van MPG
- The details of how you build a rack and how you mount stuff to the roof can make a large difference in the MPG penalty.
For mounting PV panels, clearly the lowest drag way would be to use one of the flexible PV panels attached to the van roof with adhesive. The MPG penalty for this would likely be near zero.
It appears from the test that the mounting of my single large panel close to the van roof, far back on the roof, behind the roof fan, and lengthwise rather than width wise achieved a pretty low MPG penalty.
If going for a full size roof rack, I think the details of how the rack is built could make a significant difference. Tubular racks with lots of open area should help. For the tubes that face the airstream, using elliptical tubing could help, as cylinders have a much high drag coefficient than elliptical tubes or airfoil shaped tubes. Some of the car manufacturers have picked up on this for car rack cross bars. See this video on the Yakima Whispbar.
It would be nice if one of the commercial roof rack producers would get into this, do some testing, and come out with low drag racks for the ProMaster and other like vans along with some test data to support how good it is.
Its tempting to think that doing without solar and just letting the van alternator charge the battery would save gasoline and energy, but you burn extra gasoline to generate energy with the alternator. VERY roughly: If you assume 1) 60 days of van use per year, 2) a need to generate 100 amp-hrs of battery charging per day, 3) an overall efficiency of 20% for the engine charging system, this leads to using using an extra 0.17 gallons of gasoline per day of use, or 10 gallons a year for 60 days of use, or 150 gallons for the 15 year life of the van. This is probably more than the extra gasoline used by a carefully mounted PV panel capable of generating the same 100 amp-hrs per day — and, you have all the other advantages of solar.
It seems like the energy use and carbon emissions winner is the flexible PV panel glued to the van roof.
If you know of any additional test or analysis on this subject, or have any thoughts, please leave them in the comment section.
Gary May 20, 2021
Update 12/8/2023 – Airflow Tuft Test With and Without Roof Rack
I did a further test on my van to get a better idea what the airflow around the van looks like and where the flow is attached and where separated. This test involves taping short wool tufts in a grid pattern over the outside of the van. When the van is moving, these tufts align with the flow and show the direction of the flow, and if the flow is separated (chaotic) the tufts fly in all directions and rapidly change directions.
All the details on the airflow Tuft Test…
The link above gives all the details, but one major result is that without the roof rack, the flow is attached over nearly all of the roof, and with the rack in place, the flow is separated for nearly all of the roof.
I’m beginning to wonder if the test setup is slightly flawed by the design of your roof rack. I think the issue with the rack is that it has extremely large open voids in the center that I believe will cause Helmholtz resonance and pressure oscillations. I think those oscillations will force all the airflow over the top of the van to be turbulent which is awful from a drag perspective. Are you able to dust off the old test rig and use some plywood to make an enclosed box? I think the impacts of the enclosed box would net out much closer to your theoretical 4.5% frontal area calculation than the measured 11.6% hit. In some ways, I could see an argument that protecting the maxx fan from the flow might decrease drag as well…
I’m in the process of planning a box truck build and was trying to come up with a way to mount 4x residential panels in a 2×2 stack with two panels on sliders. That’d still leave enough space for a flat mounted starlink, maxxair vent, roof hatch/skylight, and a walkable roof deck. Reducing the drag of all those components by building an enclosed “rack” is the best thing I’ve come up with at this point.
Hi Doug,
I’m sure that the airflow does separate at the forward “fairing” board and that this causes a significant increase in drag coefficient and is the main reason why the drag increase is greater than what one would expect from the frontal area increase. Some folks think of this forward “fairing” board as smoothing the flow of the air over the things mounted on the roof, but I think that it just guarantees airflow separation, lots of turbulence and a high drag coefficient. I don’t think you need Helmholtz resonance to get this – its just ordinary aerodynamics. I did the rack this way, because it is the way that most racks are done – there is often the forward fairing board and then a collection of fans, pv panels, air conditioners and rack structural members behind the fairing board. So, I think its pretty representative of a typical rack setup. I think its pretty difficult to arrange things such that the airflow sees a smooth, flat surface, but if one could do that I think it would help the drag coefficient.
I do have most of the original test rack still around and it would be interesting to try it with a flat, smooth top, but probably not going to happen very soon.
Just looking around the internet for estimates of drag coefficients of box trucks is not very encouraging – most of the sources suggest drag coefficients a fair bit high that the 0.35 that is quoted for the ProMaster in a few places – so, difference for a rack on a box truck might not be as noticeable since you base vehicle has a higher drag coefficient, but the base MPG of box trucks looks to be pretty dismal.
Gary
Yep, there’s definitely a fuel economy hit by bumping up to a box truck over a van. At least for me, the straight walls (ease of conversion and simplicity of insulation) and slightly more space (~530 cu ft in a 12’x6.5’x6.5′ box) are “worth” the fuel hit.
Rough calculations… in order to facilitate a double stack of solar panels you’d likely need ~6″ of additional height over the roof. For a standard 12’x6.5′ box that’s an increase of 5.5-6% in frontal area. If we assume some aerodynamic penalties as well and bump it up to 10% hit (taking you from ~12.5mpg to 11.25mpg) that’s an extra 1333 gallons of fuel for a 150k mile life.
For the double stack, it’d be ~1600w of installed flat mount. Estimating how much power these would generate is difficult because of the huge variance in location and time of year. Looking at two locations I’m intending to take the truck it’d be anywhere from 3-8kwh per day. Using your 0.17gallons/1.2kwh of alternator generation as a baseline, it’d be 0.425-1.13 gal of fuel to replace the solar panels. If we split the difference and assume 0.75gal/day and 60 days/yr that’s 45 gal/yr. You’d need the truck to last 30 years to be worse off than the panels… 30 years and 150k miles is only averaging 83 mi/day of use.
A single stack of panels increasing roof height by 4″ I think makes even less sense. You’re increasing frontal area by 3.5-4%, and assuming 8% total hit to aerodynamics costs you 960 gallons of fuel. Halving the alternator numbers to 0.375gal/day puts the payback period at 42.7 years. That’s about 58mi/day of use.
I suppose the other consideration is how to generate that much power with an alternator. 8 kwh at 12v would need 667Ah, even 100A would need 6hr40min of run-time. Even the minimum 3kwh at 12v needs 250Ah. Renogy’s largest 60A DC-DC charger would still need over 4hours/day of run time which isn’t realistic, you’d need to double up on chargers which would necessitate a separate alternator or you’d have to haul a generator.
The Honda EU2200i could get you to 3kwh in 1hr40min, which per the specs is a little over half a tank of fuel, call it 0.5gal/day on the low side. For the peak 8kwh it’s 4.44hr of run time and 1.32gal/day.
Unfortunately it doesn’t seem like there’s a clear option that balances convenience with efficiency.
Hi Doug,
I guess one thing you might consider would be the thin, flexible PV panels that can be glued right to the roof surface. This would be easy on a box truck with the flat roof. The drag increment for these panels would be very small. The overall performance and life of these panels might not quite be up to “real” panels, but one user on the ProMaster forum (user name Baxsie) has had them on his PM for several years and they seem to be doing well. He describes the install here: https://www.promasterforum.com/threads/flexible-solar-with-no-rack.37425/page-2#post-694555
Another option for a single layer of PV panels would be to mount the PV panels directly to the flat box truck roof. This would get the bump up down to about 1.5 inches. You would have to think carefully about how to mount the panels. Adhesive would work, but would be a bear if you had to remove the panels at some point. Fasteners would also work, but with some concern about holes in the roof.
I suppose that a lot depends on how much power you will actually need?
Gary